Energy efficiency leads to an increasing proportion of bioenergy, cutting the need for fossil fuels and reducing environmental impact. In short, energy efficiency is action on climate.
The production of pulp and other bioproducts is a process that runs entirely on energy generated in the production process.
In addition to using bioenergy in our own production, we transfer it as electricity into the grid, as heat to local industrial customers and as district heat for nearby communities. When the pulpwood arrives at the mill, it is first debarked. The bark itself is a renewable fuel. After this, the wood is chipped, and pulp cooking can begin.
“The cooking chemicals used in pulp production, along with organic material separated from the wood, are transferred to the mill’s recovery line. Energy is produced during the recovery cycle, and at the same time, the cooking chemicals are recycled and converted for reuse in pulp production,” explains Jorma Heikkilä, Development Manager at Metsä Fibre.
The combustion of wood-based organic material in the recovery boiler on the recovery line generates steam. The steam drives the mill’s turbine, producing electricity. In addition to energy, pulp production also results in biochemicals, such as turpentine and tall oil.
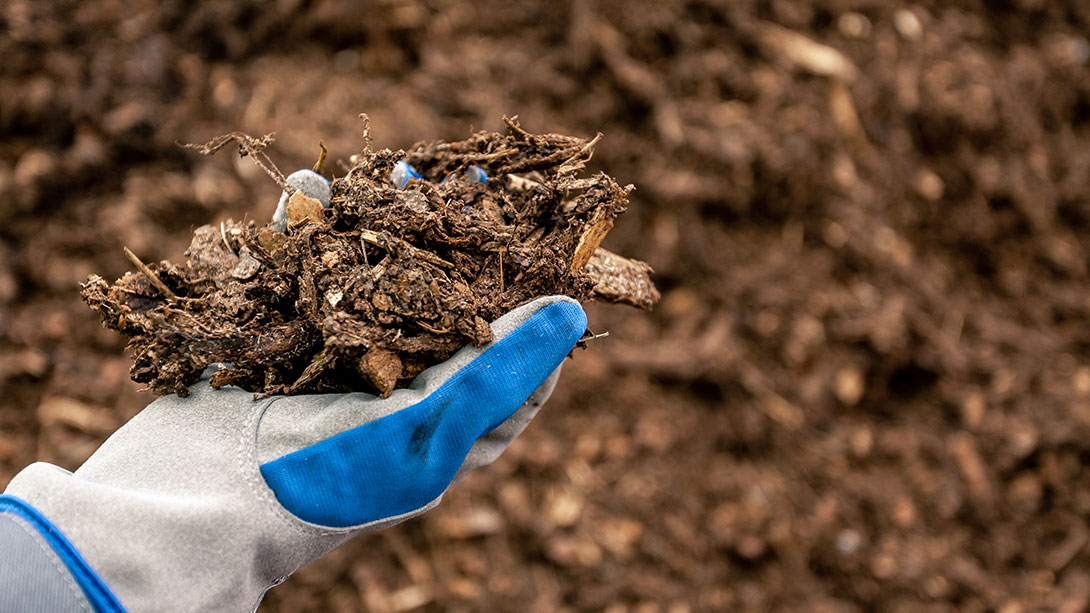
Common measures for energy efficiency
Heikkilä says that the improvement of energy efficiency at pulp mills requires constant work.
Metsä Fibre annually prepares an action plan for energy efficiency and determines the areas where energy consumption can be cut and energy production improved. It has ISO 50001 certification to ensure that steadily tougher energy directives can be met.
All mills comply with company-level guidelines, and regular training is provided to the personnel. The best practices are developed jointly – and shared with other mills.
Continuous improvement of process efficiency
Energy efficiency can also be improved by fine-tuning production practices and techniques. For example, secondary heat sources, meaning hot and warm water, are put to increasingly efficient use at the mills. At the Äänekoski bioproduct mill, heat is recovered from the flue gases and used as a replacement for steam at different stages of the process.
Combustion conditions and the latest technology, in turn, help minimise emissions to air. The mills also use purification devices, such as electrostatic precipitators and scrubbers, to control particulate emissions.
In pulp production proper, resources are used efficiently. Wood raw material is always fully utilised. Any side streams of production are utilised efficiently as bioproducts and bioenergy.
The importance of investments in new technology
Investments and new technologies provide opportunities for improving energy efficiency.
Heikkilä points out that environmental and energy efficiency is always considered when making investments and procuring equipment. Metsä Fibre mills have always actively used the latest technology in the field and continue to do so.
For example, the Äänekoski bioproduct mill uses bark gasification to produce fossil-free gas from bark for the mill’s internal use. The same gasification technology is used at Joutseno mill and will be introduced at the Kemi bioproduct mill in the future.
At the Äänekoski biogas plant, wood-based sludge goes through a digestion process resulting in biopellets and, in the future, biogas. The Äänekoski site also features a sulphuric acid plant, which has helped the mill work its way towards a closed chemicals cycle. Odorous gases are recovered and converted into sulphuric acid used in the tall oil process.
“Our guiding principle is the constant development of operations,” Heikkilä says. “The energy efficiency depends crucially on the steady operation of our mills .”