Read more about how we produce pulp
Our modern pulp mills, featuring a high degree of environmental, material and energy efficiency, produce pulp, biochemicals and bioenergy from renewable wood raw material. The raw materials, water, energy and production side streams are used efficiently and to the fullest extent possible.
Pulp is a diverse, recyclable and safe raw material for various daily products such as paperboard, tissue papers, printing papers, and specialty papers and products. It can also be used to replace fossil materials. Read more about how we convert renewable wood raw material into pulp and other bioproducts.
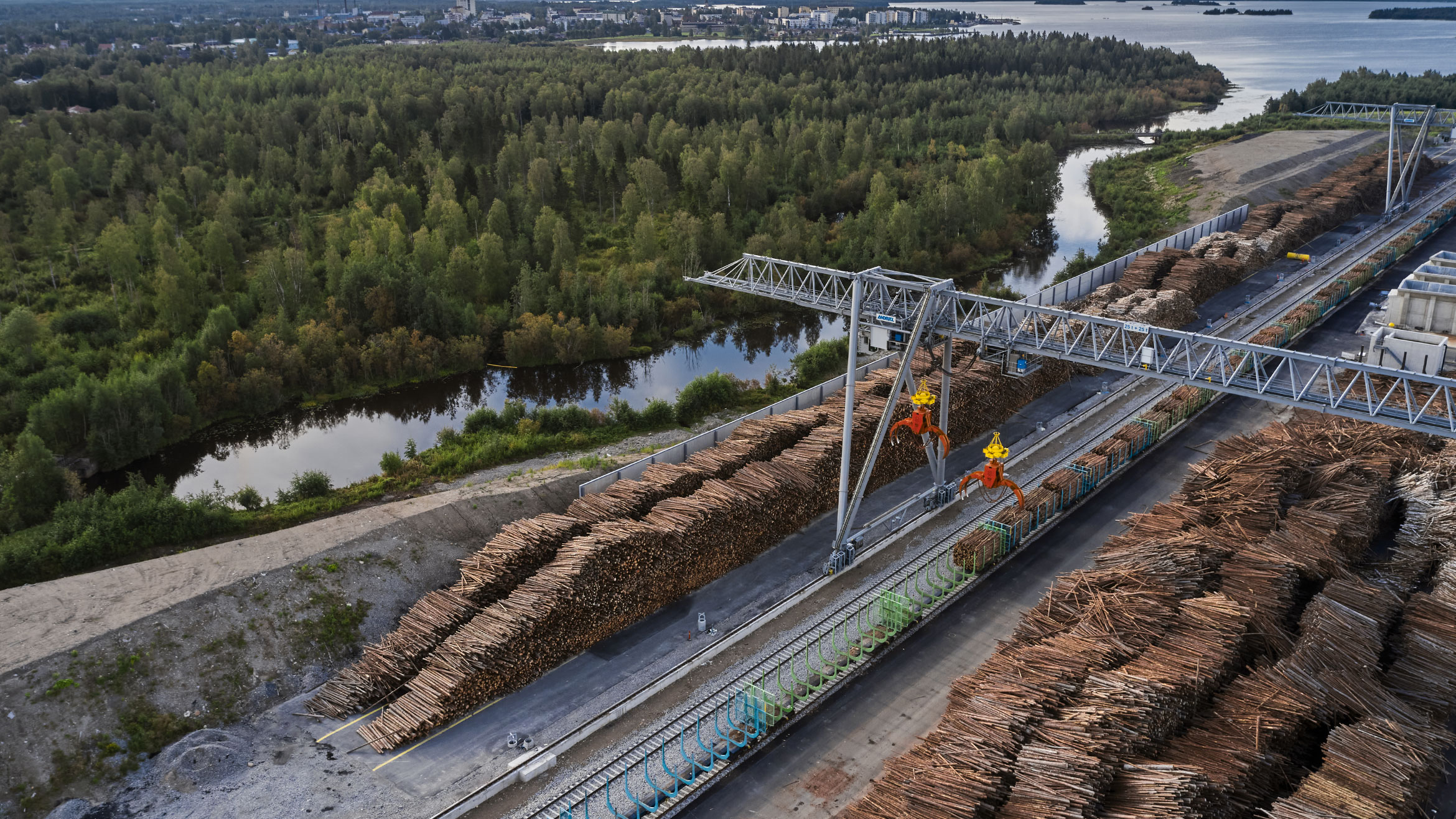
From wood to chips
The first step is to debark and chip the pulpwood sourced from sustainably managed forests. In addition to pulpwood, our mills use woodchips from sawmills. Not a single splinter of wood goes to waste: the bark of trees is used in bioenergy production. Softwood pulp is made of pine and spruce, while hardwood pulp is made of birch.
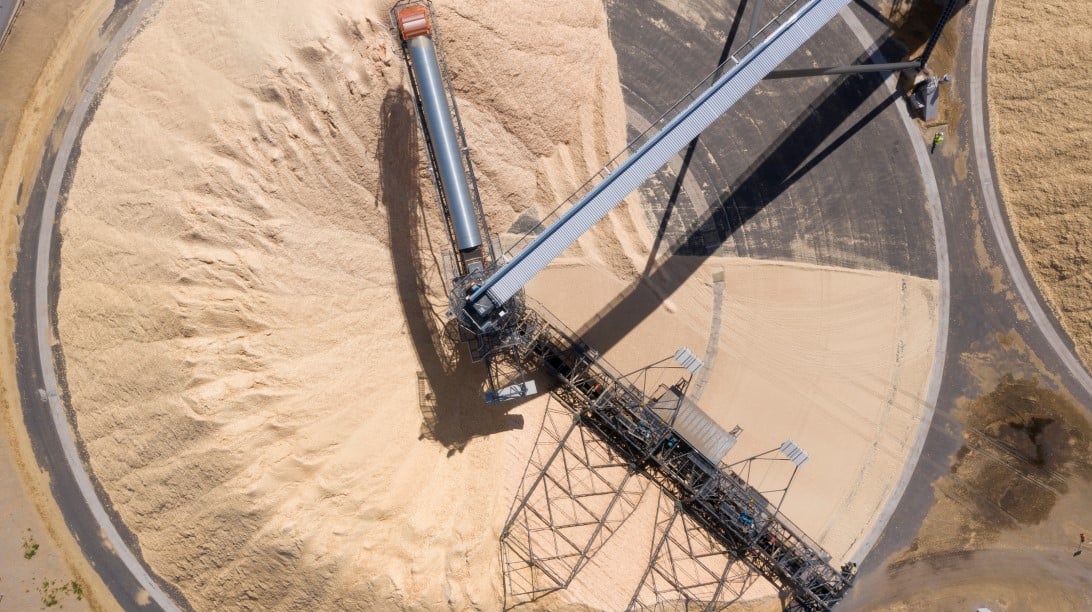
From chips to pulp
The resulting woodchips are cooked in white liquor to separate the wood fibres from the binding agents. During the cooking process, the pulp fibre gradually turns into brown pulp, which is then washed and bleached. Bleached pulp is soft and cottonlike.
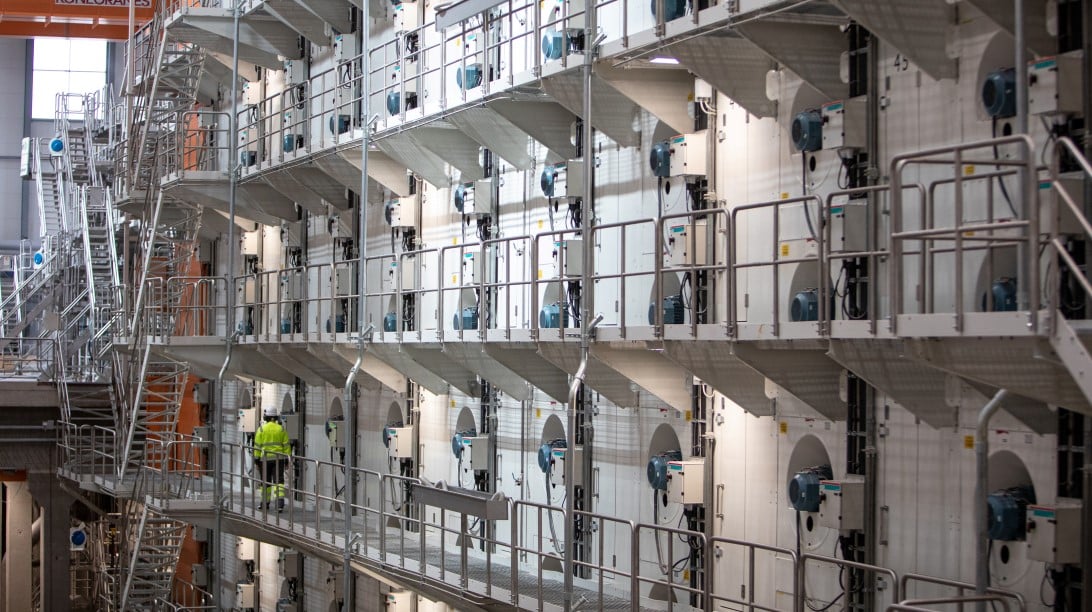
Pulp units ready for the world
After bleaching, the pulp continues to the drying department, where it is dried, cut into sheets, and baled. A bale of pulp weighs 250 kg. Bales are stacked into larger units for transport. A unit delivered to domestic customers weighs 1,000 kg, while export units weigh 2,000 kg. Each pulp unit is equipped with an RFID tag to enable customers to follow the data and delivery of the pulp batch in real time. The units are now ready to be shipped to customers.
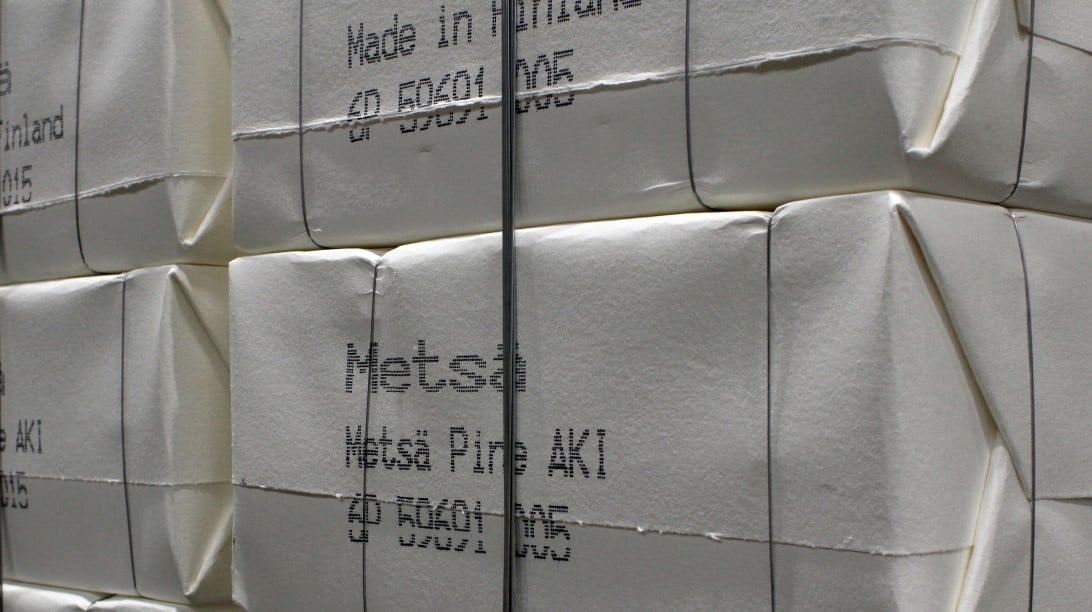
Resource-efficient production process
The raw material for pulp production and the side streams from production are used as efficiently as possible to minimise environmental impacts. Pulp production generates tall oil and turpentine as by-products. They are used as raw material for products such as fragrances, glues and paints. The lime, ash and dregs generated in the process are used as fertilisers and soil improvement agents. The aim is to make full use of all the production side streams.
The cooking chemicals used in pulp production are carefully recovered during the process. The black liquor formed from wood material and cooking chemicals is burned in the recovery boiler to produce bioenergy for our mills and local communities. This process converts the cooking chemicals into a form that can be reused in the pulping process.
The wastewater from production undergoes biological wastewater treatment before being released into waterways. The gradual isolation of waterflows and the increased degree of purification within the process have reduced the volume of wastewater, as well as the load on water bodies. The flue gases generated during the process are purified, and odorous gases are recovered and combusted.
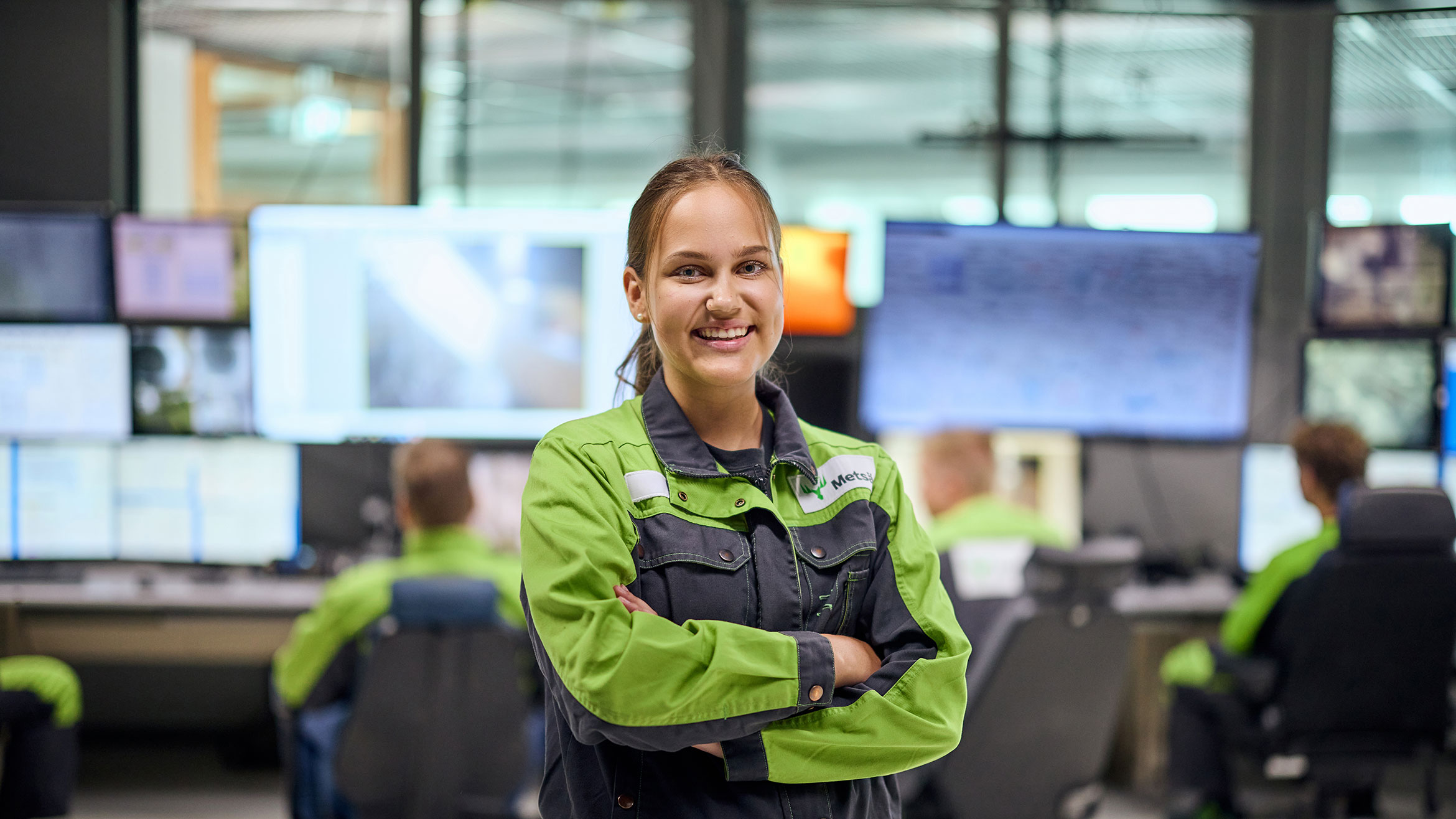
Solid competence plays a key role
The high quality of our products is based on the solid competence of our personnel. In-depth fibre expertise is crucial when the goal is to produce exactly the right types of raw materials for various end products. We also develop our pulp grades in close cooperation with our customers.
Finnish premium pulp is a highly valued export product worldwide. The pulp we produce is shipped to customers around the world.
As a raw material, pulp is well suited to a wide range of end products. Continuous development is underway to create new pulp-based innovations and products, including textile fibres, new fibre products and new packaging solutions to replace plastic.
Bioproducts production process
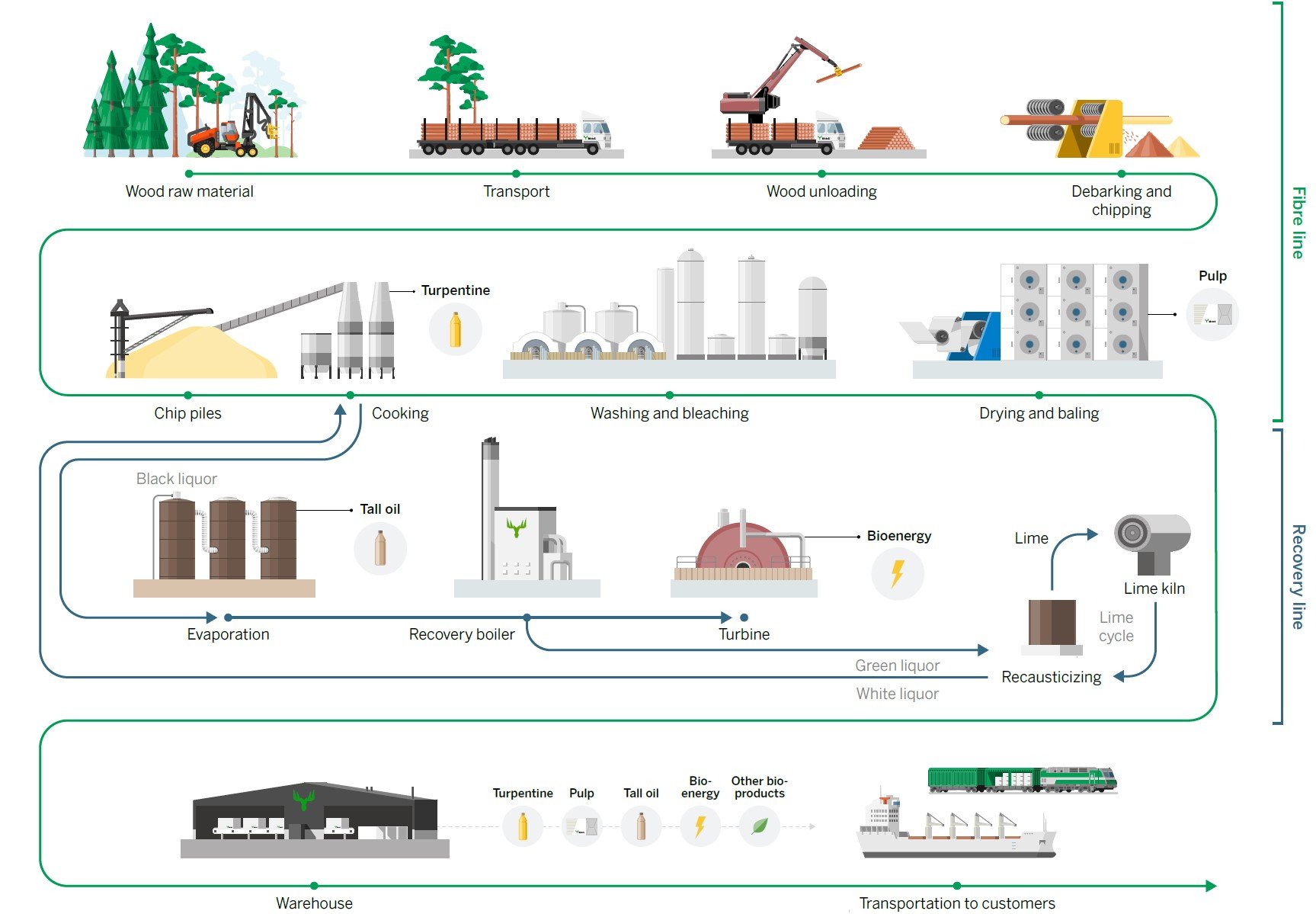