Arbo Lauri, an operator in the sawing team at Metsä Fibre’s Rauma pine sawmill, watches the massive logs move along the conveyor from the debarking section to the sawline. The logs now lined up for sawing are the sawmill’s largest to date, with a diameter up to 330 millimetres.
“We can saw up to four premium grade planks from the heartwood of a log like this. There is also enough sapwood for narrower side boards,” says Lauri.
The trunks are thoroughly examined at log reception with the aid of machine vision and artificial intelligence. The X-ray device instantly provides information about the inner quality of the trunk, including its knottiness and heartwood ratio.
Every part of the log is used. The woodchips produced at the sawmill serve as raw material for pulping at the pulp mill in the same mill area, while the bark and the sawdust are used for generating power.
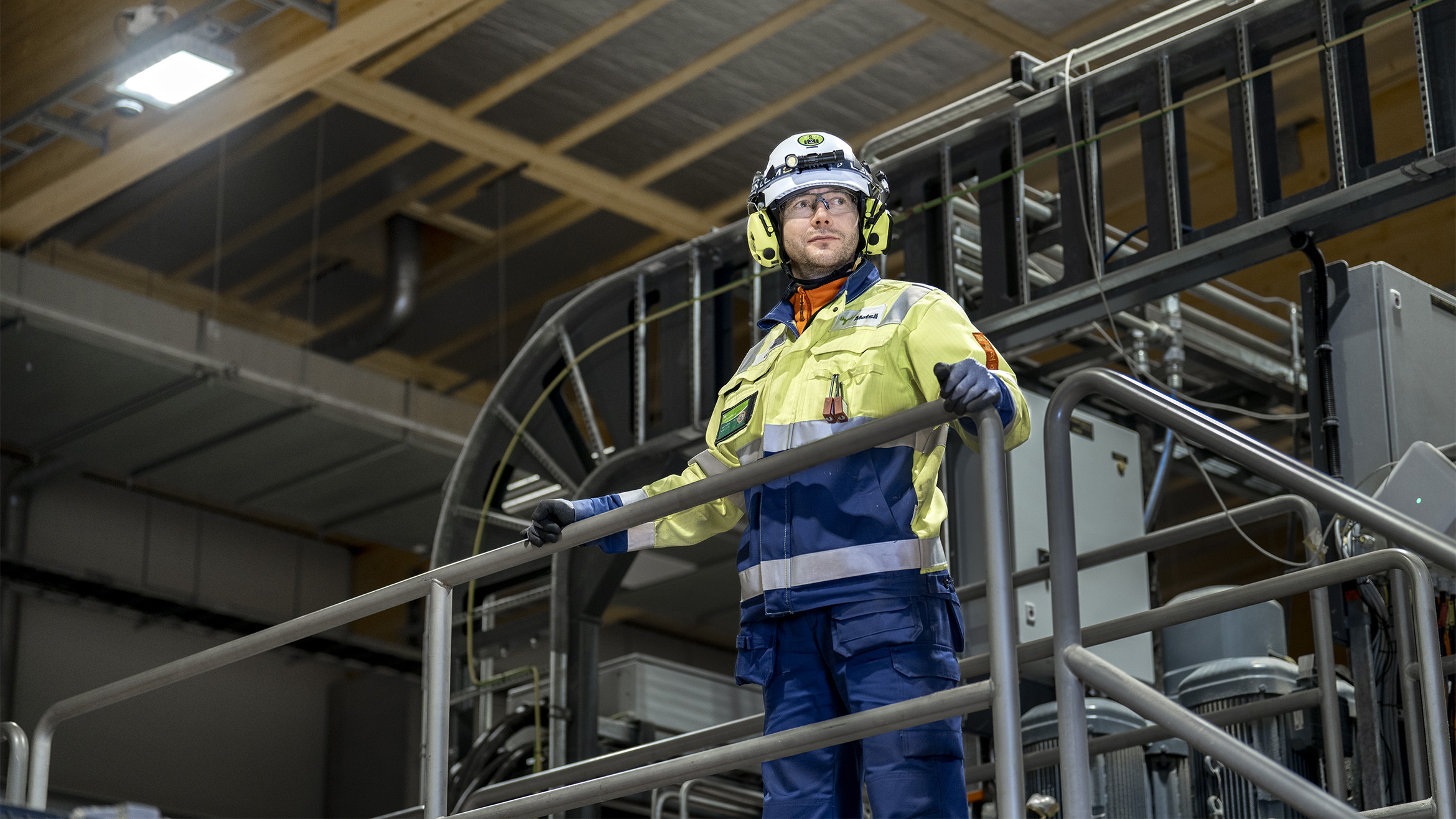
Maximum 250 metres per minute
The area for which Lauri’s sawing team is responsible stretches from the sawmill infeed to the debarking department and the sawline. Each shift has two operators. During their shift, the team members monitor their area of responsibility in the sawmill’s control room, which is shared with operators from other teams. They also make field trips alongside control room work.
The sawline is visible proof of Rauma’s role as a frontrunner. At the beginning of the line, the log is rotated into the best possible position for sawing. This is the first place in the world to have introduced the dx, or pre-sawing, process.
“It means making a pre-cut before actually sawing off the pieces. It facilitates first-class surface quality, dimensional accuracy, and high sawing speed in all log grades.”
The sawline’s speed is optimised, for example according to the thickness of the log to be sawn, and the goal is to reach a maximum speed of 250 metres per minute. This is triple the speed of a conventional sawline.
Lauri finds the efficiency and speed motivating.
“I enjoy watching the sawline run at full speed with everything working smoothly. It requires continuous finetuning in the background,” he says.
We aim to make such good sawn timber that we would buy it for ourselves.
Operators control quality throughout the process
Lauri’s career at Metsä Fibre began at Kyrö sawmill in 2006, and he was among the first applicants to Rauma.
Lauri holds a further vocational qualification as well as a specialist vocational qualification in sawmill work. Operators at Rauma sawmill must have a keen interest in learning new things. The three-shift operation poses its own demands. The sawmill runs in three shifts seven days a week – another departure from the traditional practices of Finland’s sawmill industry.
Thanks to automation, the operators now have more time for quality control. Ultimately, it is the operators’ experience and sensory quality control that ensure that sawn timber shipped worldwide from Rauma sawmill matches what the customer has ordered.
“For us, quality means regular measurements. Visual inspections by the operators are also required. This applies to both the sawing result and the machines, because a blade that is in poor condition can easily leave an ugly mark on the surface of the wood.”
The operators change the blades together at the sawmill. LSAB, the sawmill’s partner, services and sharpens the blades to be fit for reuse.
The premium quality of sawn timber is important for the operators. It is a question of professional pride.
“We aim to make such good sawn timber that we would buy it for ourselves,” says Lauri.
Experts and all-rounders by training
In green sorting, recently sawn products move in good order along the two long sorting lines, controlled by sorting robots and machine vision. The pieces on the line are also examined by Pekka Lappalainen, an operator in the sorting team.
Formerly an electrician by training, Lappalainen completed a further vocational qualification in sawmill work when he moved to Rauma. The training increased his knowledge not only of sawing operations but also of sawmill maintenance and technology.
Understanding and using new technology require a great deal of learning. Metsä Fibre has invested in the training and orientation of operators. Operators also participated in on-the-job training at different sawmills. All this together provides them with deep competence. In addition, they must understand the entire sawmill process, as the future goal at Rauma sawmill is a model in which proficient multiskilled operators handle the tasks of several teams.
Multiskilled people like Lappalainen were actively sought for Rauma sawmill during recruitment. With its varied experience, the team of operators can jointly solve challenges in the best possible way.
Problem solving is what Lappalainen enjoys most in his work. His training as an electrician is valuable, for example in determining the reason for possible device failures.
“Being able to solve a fault or problem or adjust the trimmer’s calibration is rewarding”, he says.
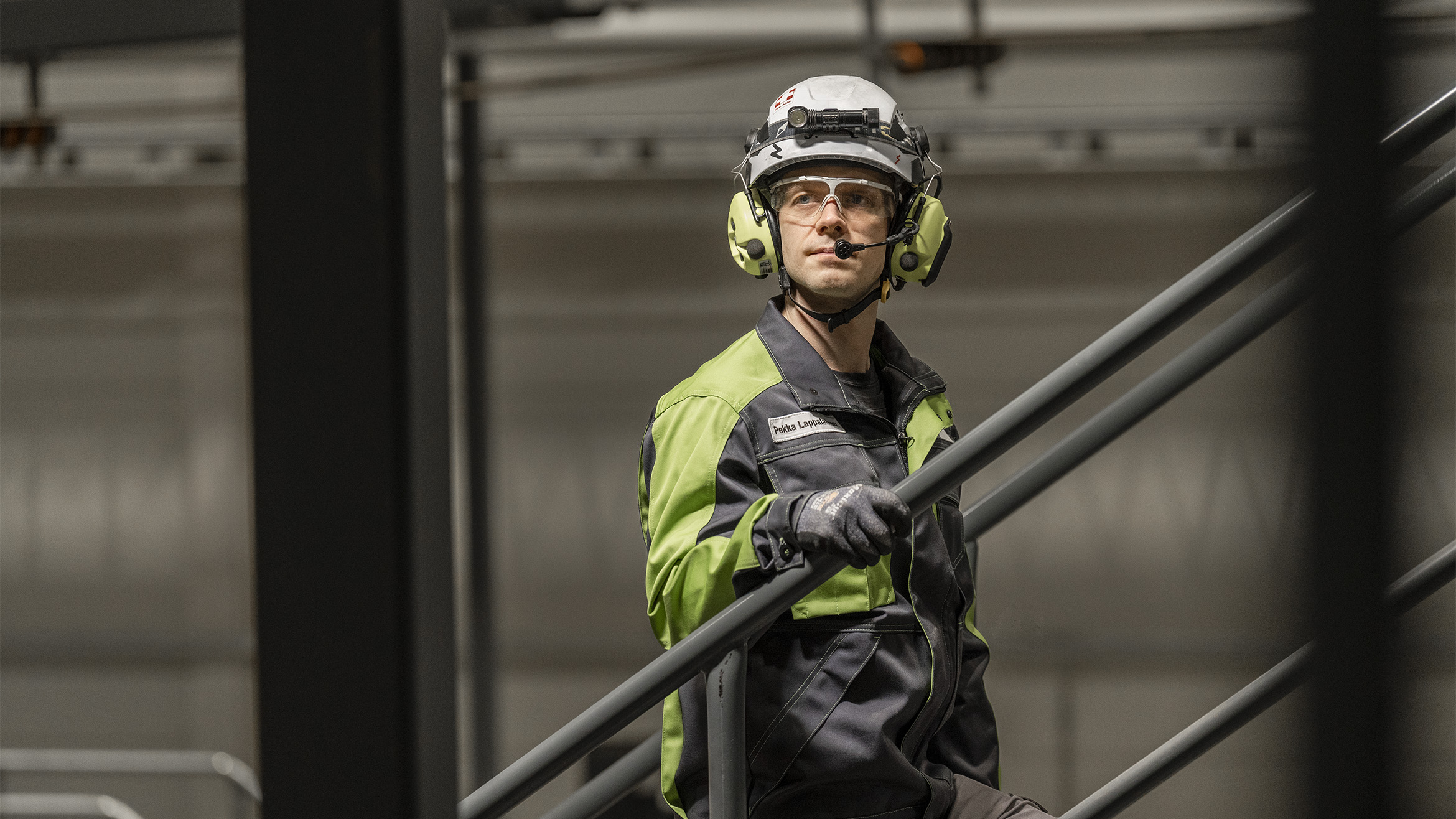
All-rounders like Pekka Lappalainen have been intentionally selected for Rauma sawmill.
One millimetre can be crucial for quality on the sorting line
“Quality assurance is our team’s most important task. Any product that does not meet requirements must be removed from the process as early as possible,” says Lappalainen.
In green sorting, sawn timber is sorted according to its dimensions. Automation makes this fast and efficient. The sorting team’s operators check the dimensions manually from time to time, so they must always have callipers and tape measures to hand.
“The line is equipped with precise cameras, but operators are also required to intervene in the process if the situation calls for it. Also, no sawing flaws such as blade marks or missing pieces are allowed in the boards. Planing must be done to a precision of one millimetre, so you really must pay close attention.”
The green sorted sawn timber moves on to the sticking plant and drying department, and after drying to dry sorting, where the team also checks the quality of sawn timber. Thanks to the state-of-the-art technology used at the sawmill, quality data can be collected throughout the process.
Aiming for perfect sticker stacks
In the sticking plant, sawn timber is piled into high stacks for drying. A machine places narrow timber stickers of specifically determined dimensions between the layers of products. These stickers ensure that air circulates as evenly as possible around the sawn timber that has been stacked to dry.
“The sticker stacks must be perfect for drying to be successful. The stickering of different size products is a demanding task,” says Riku Tamminen, an operator in the stickering and drying team.
“At Rauma sawmill the sticking plant is connected to the kiln drying department. This means our team is responsible for both phases, and we can affect the drying process by what we do in the sticking plant. It is motivating, and the variety of the work holds your attention,” he adds.
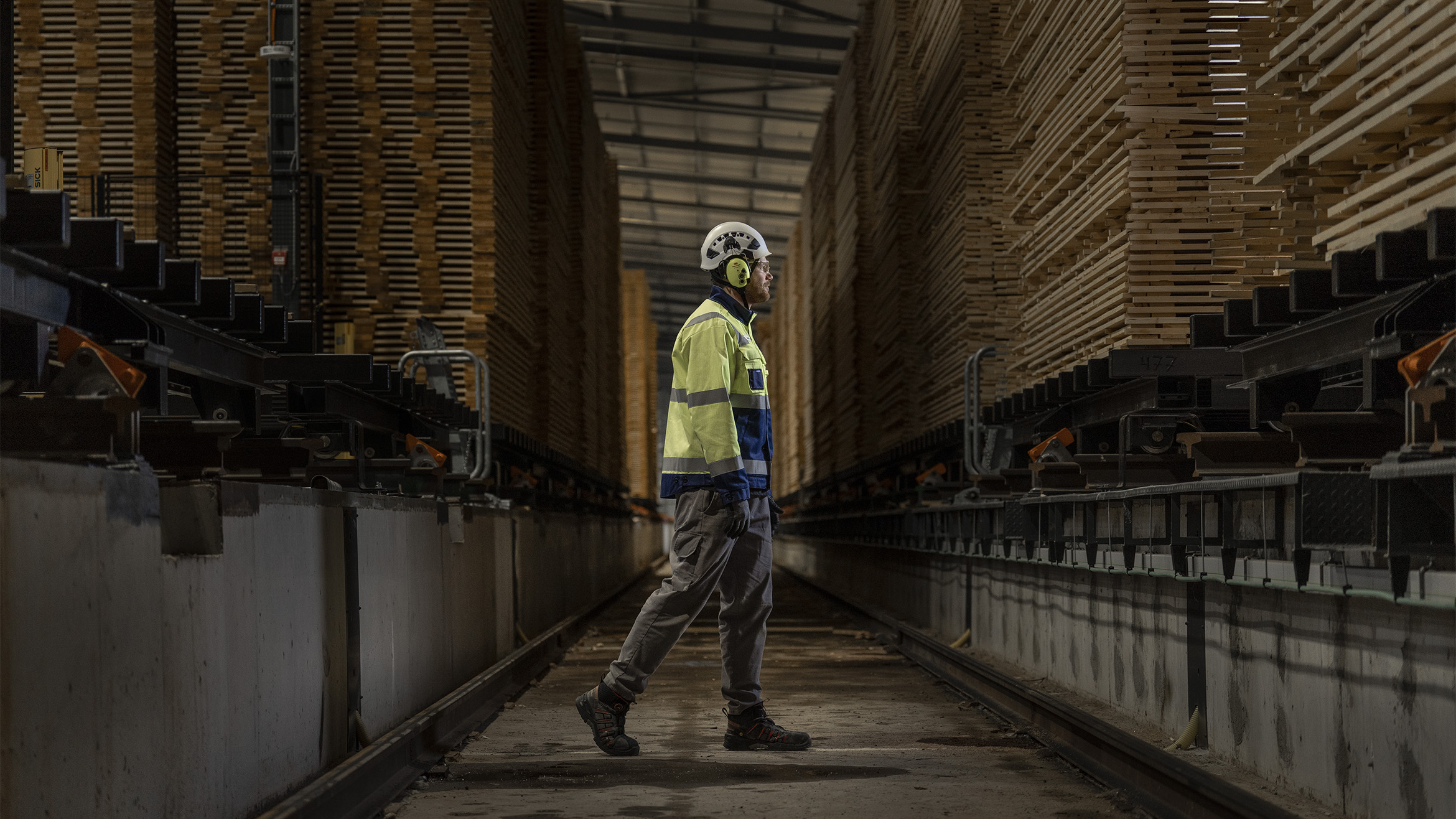
Precise drying refines the quality of sawn timber
In the kiln drying department, sticker stacks extending from the floor to the ceiling form impressive alleys in the hall. The size of the building is also impressive, covering approximately two hectares. The halls contain nine continuous channel driers and 26 chamber kilns. The heat needed in the drying process is obtained from the pulp mill that is part of the integrated mill.
Precise drying refines the quality of sawn timber. It requires time; products that have been dried too quickly may crack. Drying is based on drying formulas, which determine how the air temperature and relative humidity are regulated. The moisture content varies from approximately 17 per cent, typical of shipping-dry sawn timber, to 10 per cent for extra-dry grades.
Drying is always designed to suit the intended end product. Customers must be able to trust that products such as windows and doors made from sawn timber produced in Rauma will retain their shape in demanding climate conditions.
“In the woodworking industry the right moisture content is critical. We invest in quality. It shows the results of our work,” says Tamminen.
Rauma sawmill’s model of a single control room is the first of its kind in the history of sawmilling.
Automated loading is new in the sawmill industry
Grade-sorted sawn timber is ready for packaging. The pressing device squares off the ends of the sawn timber bundles and ties them with a hoop. The next machine in line slips a protective hood over the package.
Jari Trygg is one of the operators on the packaging team. His team is responsible for ensuring that the sawn timber is of the right dimensions, and that the packaging looks as it should.
The conveyor lines automatically carry the sawn timber bundles to the lorry waiting by the door at the far end of the hall. Thanks to automation, operators can concentrate on supervising the loading process and ensuring the quality of the sawn timber packages. Safety at work has improved now that forklifts are no longer used to move packages.
The control of the automated loading process is linked to the sawmill’s control system, so loading can be monitored from the control room. The system also allows waybills to be submitted automatically to the customer, port, transport company and loading system supplier.
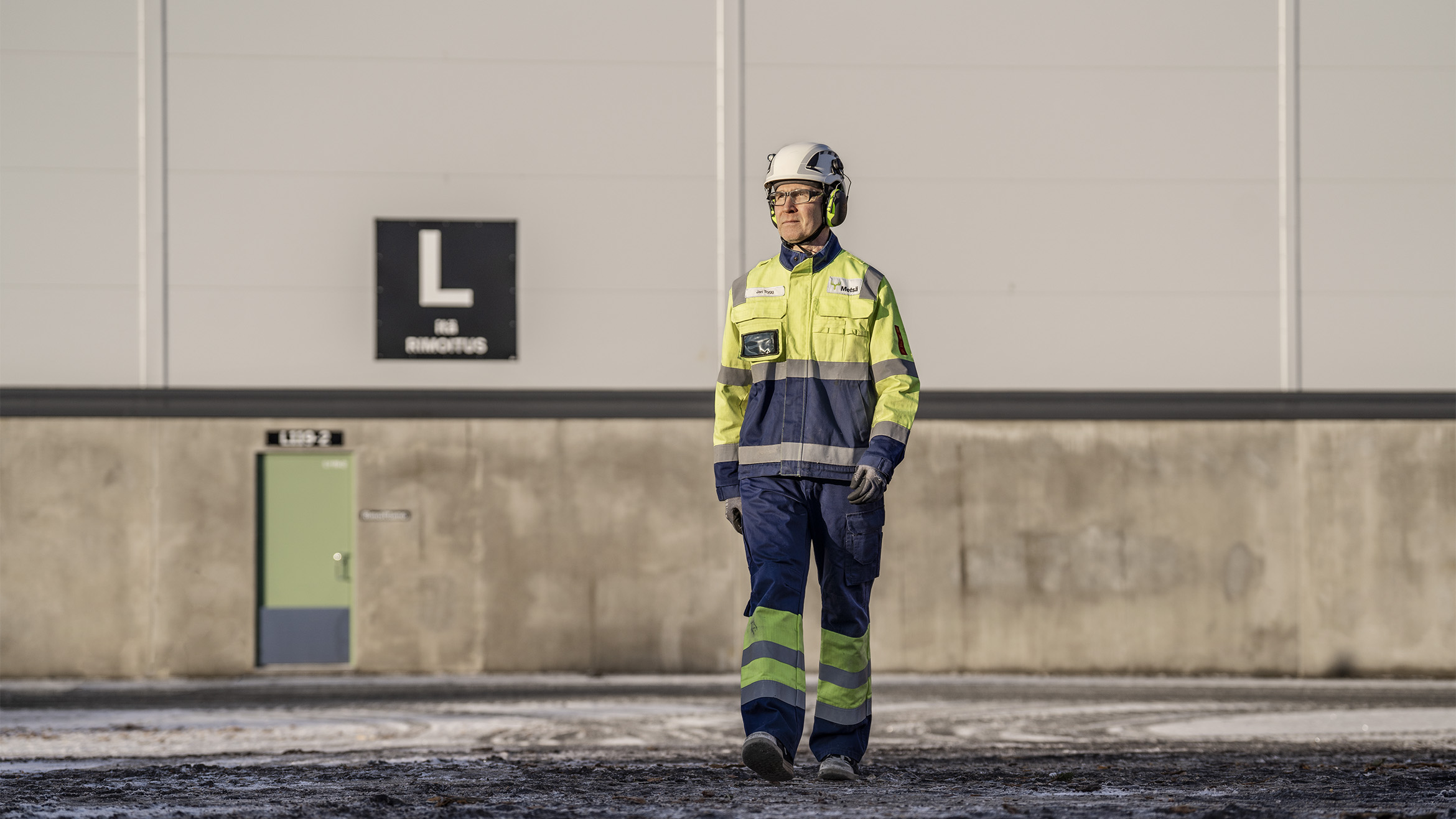
Praise for good team spirit
Trygg and the rest of the packaging team are responsible for ensuring that packages leave the sawmill as smoothly as they were produced. Specially equipped lorries pick up packages from the sawmill in three shifts.
“The sawmill has no warehouse for finished sawn timber. The packaged products are transported immediately to the Port of Rauma, a few kilometres away,” says Trygg.
Before transferring to Rauma, Trygg worked at a paper mill for 37 years. He is relatively new to the sawmill industry, but his long career gives him calmness and confidence.
Like all the other operators, Trygg speaks warmly about the team spirit. The operators in the central control room help and learn from one another. They all share the same goal: to ensure that nothing but premium sawn timber is shipped to the world from Rauma sawmill.
This article was originally published in Timber Magazine issue 2023.